Catalytic hydrotreating is a hydrogenation process used to remove about 90% of contaminants such as nitrogen, sulfur, oxygen, and metals from liquid petroleum fractions. These contaminants, if not removed from the petroleum fractions as they travel through the refinery processing units, can have detrimental effects on the equipment, the catalysts, and the quality of the finished product. Typically, hydrotreating is done prior to processes such as catalytic reforming so that the catalyst is not contaminated by untreated feedstock. Hydrotreating is also used prior to catalytic cracking to reduce sulfur and improve product yields, and to upgrade middle-distillate petroleum fractions into finished kerosene, diesel fuel, and heating fuel oils. In addition, hydrotreating converts olefins and aromatics to saturated compounds.
Hydrotreating for sulfur removal is called hydrodesulfurization. In a typical catalytic hydrodesulfurization unit, the feedstock is deaerated and mixed with hydrogen, preheated in a fired heater (600°-800° F) and then charged under pressure (up to 1,000 psi) through a fixed-bed catalytic reactor. In the reactor, the sulfur and nitrogen compounds in the feedstock are converted into H2S and NH3. The reaction products leave the reactor and after cooling to a low temperature enter a liquid/gas separator. The hydrogen-rich gas from the high-pressure separation is recycled to combine with the feedstock, and the low-pressure gas stream rich in H2S is sent to a gas treating unit where H2S is removed. The clean gas is then suitable as fuel for the refinery furnaces. The liquid stream is the product from hydrotreating and is normally sent to a stripping column for removal of H2S and other undesirable components. In cases where steam is used for stripping, the product is sent to a vacuum drier for removal of water. Hydrodesulfurized products are blended or used as catalytic reforming feedstock.
Hydrotreating processes differ depending upon the feedstock available and catalysts used. Hydrotreating can be used to improve the burning characteristics of distillates such as kerosene. Hydrotreatment of a kerosene fraction can convert aromatics into naphthenes, which are cleaner-burning compounds.
Lube-oil hydrotreating uses catalytic treatment of the oil with hydrogen to improve product quality. The objectives in mild lube hydrotreating include saturation of olefins and improvements in color, odor, and acid nature of the oil. Mild lube hydrotreating also may be used following solvent processing. Operating temperatures are usually below 600° F and operating pressures below 800 psi. Severe lube hydrotreating, at temperatures in the 600°-750° F range and hydrogen pressures up to 3,000 psi, is capable of saturating aromatic rings, along with sulfur and nitrogen removal, to impart specific properties not achieved at mild conditions.
Hydrotreating also can be employed to improve the quality of pyrolysis gasoline (pygas), a by-product from the manufacture of ethylene. Traditionally, the outlet for pygas has been motor gasoline blending, a suitable route in view of its high octane number. However, only small portions can be blended untreated owing to the unacceptable odor, color, and gum-forming tendencies of this material. The quality of pygas, which is high in diolefin content, can be satisfactorily improved by hydrotreating, whereby conversion of diolefins into mono-olefins provides an acceptable product for motor gas blending.
Feedstock |
From |
Process |
Typical products – to – unit |
Desulfurized naphtha |
Coker |
Rearrange, dehydrogenate |
|
Naphthene-rich fractions |
Hydrocracker, hydrodesulfur |
Rearrange, dehydrogenate |
|
Straight-run naphtha |
Atmospheric fractionator |
Rearrange, dehydrogenate |
|
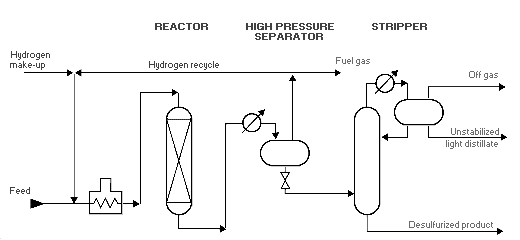
Schematic of distillate hydrodesulfurization
Excessive contact time and/or temperature will create coking. Precautions need to be taken when unloading coked catalyst from the unit to prevent iron sulfide fires. The coked catalyst should be cooled to below 120° F before removal, or dumped into nitrogen-inerted bins where it can be cooled before further handling. Special antifoam additives may be used to prevent catalyst poisoning from silicone carryover in the coker feedstock.
There is a potential for exposure to hydrogen sulfide or hydrogen gas in the event of a release, or to ammonia should a sour-water leak or spill occur. Phenol also may be present if high boiling-point feedstocks are processed.
Because of the operating temperatures and presence of hydrogen, the hydrogen sulfide content of the feedstock must be strictly controlled to a minimum to reduce corrosion. Hydrogen chloride may form and condense as hydrochloric acid in the lower-temperature parts of the unit. Ammonium hydrosulfide may form in high-temperature, high-pressure units. See Ammonium Bisulfide corrosion Page in this web site.